As a top hydraulic press manufacturer, PressMaster is proud to provide you with high quality equipment at competitive prices. The following offers you a quick overview of the process of stamping, as well as the dies used in your hydraulic press.
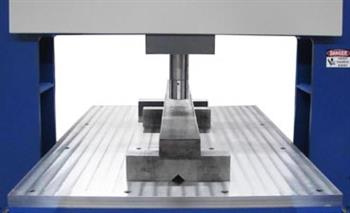
Understanding Stamping
A stamping press is simply a metalworking machine tool that can be used to cut or alter the shape of metal by deforming it using a die. Located inside the stamping press window, the die, or tooling, is the center of all the action when stamping is being completed. Energy created by the
hydraulic press movement produces a part of sheet metal that can be cut, pierced, trimmed, or bent. Tooling even has the ability to insert nuts or other parts of hardware, weld, and tap when specialized elements are added.
A Look at Die
Essentially, die is composed of two parts, the die cavity and the die punch. All parts necessary for cutting and forming a stamped part lay on a metallic plate referred to as a die shoe. To form a complete die set, you must have two die shoes. In most cases, this includes a lower die show and an upper die shoe.
The size of a die is dependent upon the type and size of the part being stamped, as well as the type of work that must be performed to create that specific part. Die can be as small as a few inches in length and height when used to produce electrical components or as large as 6 feet high and 10 feet long, such as when it is used to create automotive panels. However, the size of the die is limited by the window opening size on stamping machine.
Stamping presses are available in a variety of configurations and types at PressMaster, including
C frame press,
H frame press, and more.
How Are Die Created?
Designing and constructing dies can be an expensive and time consuming process. In most cases, dies are composed of parts including springs, punches, and pins, that are attached to the die base. The parts of the die, such as the punch, are at risk for breakage due to frequent wear and tear. In the past, this could result in the shutdown of shop presses while arrangements were made for repair. This significantly slowed down production, while increasing the overall cost of the stamping process.
The Cost of Stamping
Stamping can be rather expensive and any breakdown in a hydraulic press can be time consuming. As a result, PressMaster has taken every step possible to ensure that we only manufacture the highest quality metalworking machinery. We are dedicated to making every effort to protect the tooling in all of our hydraulic presses. We are proud to be able to specialize in creating custom shop presses that include all the features needed for your project. Whatever your needs are, we can accommodate them.